In the last 2 years IFB teams succeeded to save 32% of water per ton produced. How did we do ? The following article presents our water consumption reduction strategy.
Insulating Fire Bricks are mostly made of refractory clays with a high content of silica and alumina. An organic filler like saw dust is added. It will disappear at firing to create the porosity of the brick. Finally water is added to the mixture.
In the insulating fire bricks manufacturing process, water allows to set the right level of humidity for the mixture. Humidity acts as a natural binder between the different particles required for the mixture. It will also provide the needed plasticity to shape the bricks in a precise and repetitive way. A little bit further in the process, during the drying phase, water will be carefully removed from the bricks. This will enable the proper high temperature firing. No water is used at any other step in the process. Therefore no industrially polluted water is released from the factory.
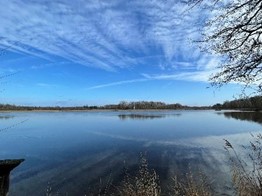
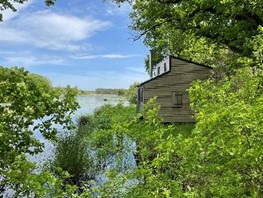
Being a century old Living Heritage Company, IFB REFRACTORIES has inherited its processes from a time when resources were scarcer. This results in today’s healthy foundations for resource-efficient manufacturing.
For example, our key raw materials spend a long time outdoors to naturally absorb a high level of humidity from rainwater. This allows only the minimum amount of water to be added during manufacture.
Healthy foundations are key, but must be coupled with optimisations along the whole manufacturing process. Yield, dimension and quality Improvements, along with regular monitoring lead to substantial water consumption savings in the manufacturing process.
On top, rainwater is collected from our roofs to further reduce the consumption of running water. Other important projects are also underway to keep improving. This is probably just a drop in the ocean at worldwide scale, but a significant contribution at local level.
Get in touch if you want to know more about our bricks